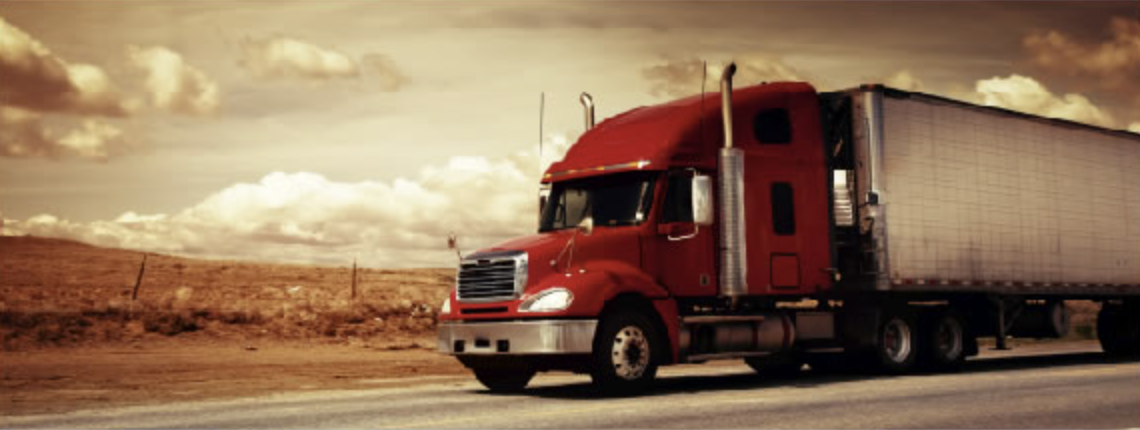
Fleet Concerns for 2023 – Issue #3: Aging Assets/Maintenance Needs
This is the third blog in a series expanding on the issues fleets are facing covered in the January blog by Dean Vicha, President of NationaLease.
My last blog addressed supply chain issues and tightening allocations which leads logically into this topic: the older the truck, the bigger the potential maintenance issues. According to Dean’s blog, even though there might be some loosening up as far as allocations, many fleets “are probably on average a year to a year and a half older than we would normally want them to be.”
So, faced with this reality and the fact that, without more availability, existing assets may become increasingly unsustainable, fleets have to be smarter, more efficient, and more proactive when it comes to maintenance practices and performance. Over the last year, I’ve written a number of blogs, both here and on my IdeaXchange blog page about the increasing importance of maintenance procedures, protocols, and personnel. Below are just some of the steps fleets need to take to ensure that their older assets can maintain productivity until new replacement vehicles arrive.
Scheduled maintenance
Every fleet should have its regular preventive maintenance (PM) schedule to maintain all the assets in the fleet to keep them running and to prevent or reduce downtime. How often that occurs should be assessed on a truck-by-truck basis. Deciding when an individual truck needs scheduled maintenance depends on a number of factors: the age of the truck; the mileage traveled regularly; environmental issues (trucks that operate in colder climates will need different maintenance to address the wear and tear on a truck due to snow and ice conditions); usage patterns; and more. Although no truck should miss its assigned schedule, it is sometimes unavoidable. As I note in my blog on this subject, maintenance managers need to have a system that will track the compliance of each asset. Should a truck miss its scheduled appointment, a new time will be set up.
Predictive maintenance
The best way to avoid downtime is to solve a problem before it actually becomes a problem. Where preventive maintenance follows a specific planned schedule, predictive maintenance uses real-time data to ensure maintenance occurs as needed, ensuring that problems are handled before they interrupt operations. As a recent FleetOwner article notes, predictive maintenance “can help fleets avoid unscheduled vehicle downtime by creating a vehicle health profile based on received diagnostic trouble codes and using data analytics to measure that against historical data.” This requires a software platform and the personnel that know how to use and decipher the data, which can be a challenge for smaller fleets but the benefits of reduced downtime and less expensive repairs would be worth the cost. The article also cautions maintenance managers to not fall victim to data overload. Too many fault codes can be overwhelming, but as I noted in a recent blog, “Fleet managers need to be able to determine which require immediate action and which can wait to be addressed or even deferred until the next scheduled maintenance service.”
Track and measure maintenance KPIs
Maintenance managers need to monitor the fleet by setting up Key Performance Indicators (KPIs) to measure performance. Four of the KPIs to consider: (1) How many miles does a component function before it needs to be replaced. This is especially true for items like tires and brakes that get lots of wear; (2) If a vehicle is in the shop between PM services, managers need to explore why: Missed appointment? New route deployment? Technician missed something; (3) Track the number of on-road breakdowns. If too many occur, see if there’s a pattern that points to a vehicle or personnel issue; and (4) Look to your drivers who know the vehicle as well as anyone. Look at the driver’s Daily Vehicle Inspection Report. For more details on what to look for, read my blog on this topic.
Commit to ongoing training of personnel
Fleets continue to experience shortages of qualified drivers and technicians. If you’re fortunate enough to have a good team, you want to retain them. One of the ways to do that is to offer ongoing training to keep up with new diagnostic equipment and tools. Trucks are much more complex and technology-enabled than ever, so your diesel techs (and at some point, EV techs) need to keep pace with all of those advances. You need to do the same for your drivers who are the first line of defense when something doesn’t feel right. It’s important to include drivers in their own training courses.
Dedicated contract maintenance can relieve the burden
If transportation is not your core businesses; if your fleet serves only as a way to get your product to its destination, then you might consider outsourcing your fleet maintenance. NationaLease Contract Maintenance lets you maintain control of your fleet without the expense of keeping an on-site shop, excess inventory, and increased head count due to seasonal variability. Our contract maintenance does a lot more than simply maintain and repair your assets. Knowing approximately what your annualized maintenance costs will be will give your organization greater control over its working capital to grow the business and move forward.
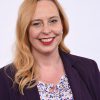
About Jane Clark
Jane Clark is Vice President of Member Services for NationaLease. Before joining the full service truck leasing organization, she served in executive positions with some of the nation’s top staffing and recruitment agencies.