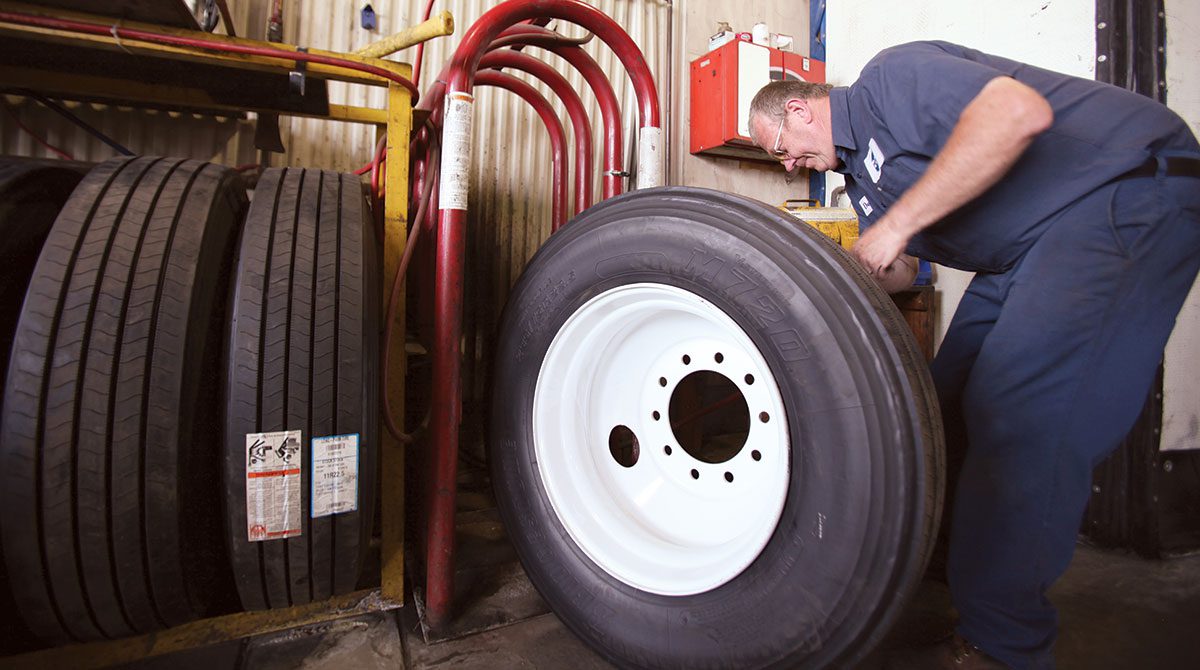
When It Comes to Parts Inventory, Be Proactive
Last month, a headline in a CDL Life article stated “Five days into 2022 and some dealerships are already out of semi trucks for the year.” Although this article referred to dealers in Kansas, the reality is that fleets are facing this shortage all across the U.S. and Canada. This crisis has made maintaining the vehicles you have more important than ever. But the shortage isn’t just the trucks themselves; parts also are in short supply. So, what can fleet managers do to mitigate this problem?
Think ahead, plan ahead
A June 2021 article in Truckinginfo.com noted that having a truck down due to a lack of parts can cost a fleet between $800 and $1,000 per day. But all is not hopeless. There are definite steps that fleets can take to manage their parts inventory. In the article, industry writer Denise Rondini offers eight steps fleets should be undertaking. Below are just some of those recommendations:
- Depend on data – To optimize your fleet in these trying times, it’s vital to have as much accessible data as possible on every vehicle in the fleet, including make, model, and maintenance history. When keeping maintenance records, it is essential to note the type of maintenance undertaken and the parts (if any) used in each instance.
- Rely on VMRS codes – Whether a dealer/distributor doing the parts ordering is in sunny Miami or cold Calgary, the needed parts numbers are standard, thanks to Vehicle Maintenance Reporting Standards (VMRS) codes. Although the codes don’t necessarily address the shortage, they do make ordering easier and faster…and quick response matters when a truck is down.
- Keep count of inventory – Whether it’s doing a physical inventory on a regular basis, or entering information into the company computer, fleets need to know what they have on hand at any given time. Records allow fleets to see which parts are used most frequently and make sure to order enough to withstand shortages. The records also allow fleets to see which parts are rarely needed and keep minimum amounts of those.
- Think ahead, plan ahead – Thanks to AI and machine learning, fleets are now able to predict what parts will be needed and when. This technology also gives them the data necessary to identify potential problems when it comes to parts shortages and their own inventory needs. Knowing this enables maintenance to look for alternative replacement parts and not be caught short. Fleets also need to really look closely at inventory levels and take into account these shortages. This may necessitate having more inventory on hand for parts that will take longer to source and deliver.
- Set your sights on suppliers – In today’s market, parts suppliers play a major role, so having good relationships with them is important. This holds true whether you deal with a parts manufacturer directly or purchase through a distributor. It’s also smart to work with suppliers that have a larger network. That way, if the store or distributor you normally deal with doesn’t have a particular part in stock, they are able to identify that part availability at another location and have it shipped to you.
Even though none of these steps can end the shortage, they can definitely put your fleet in a better position to withstand the issue…and keep your vehicles road-ready until the shortage subsides.
For more details and more steps to take, read the full article.
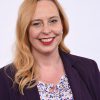
About Jane Clark
Jane Clark is Vice President of Member Services for NationaLease. Before joining the full service truck leasing organization, she served in executive positions with some of the nation’s top staffing and recruitment agencies.